News
Understanding the Ins and Outs of Lean and Six Sigma Principles for Your Small Warehouse

Published
12 months agoon
By
Watson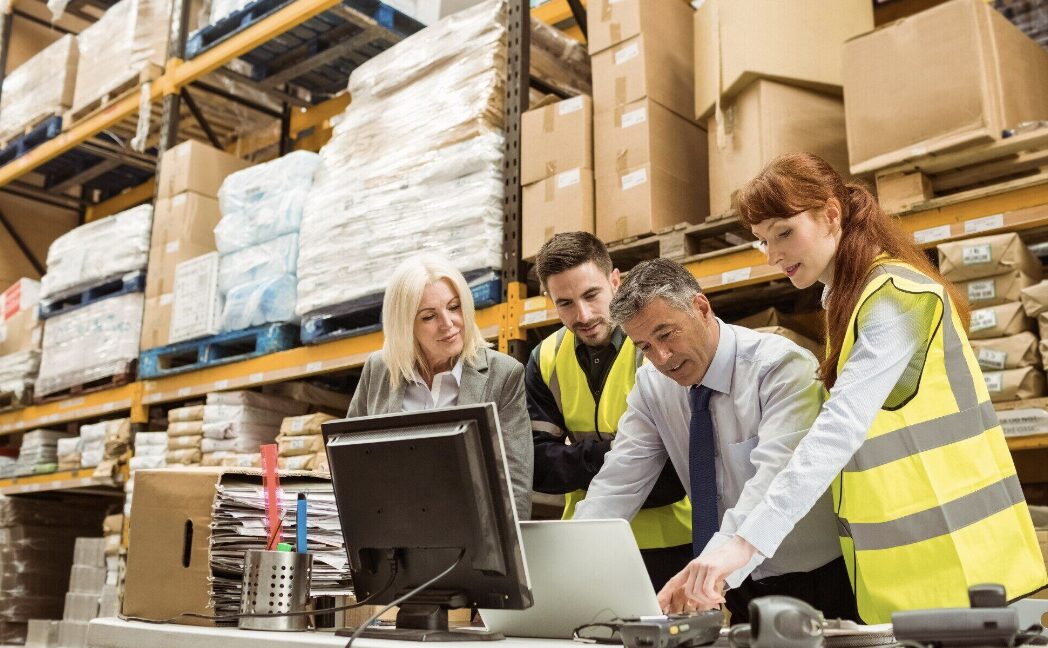
In today’s dynamic market, efficiency is the lifeline for small warehouses. Are you leveraging Six Sigma principles in your operations? This method, rooted in defect reduction and quality improvement, can be a game-changer.
Many small warehouse owners overlook its potential impact. Yet, when applied correctly, these principles can streamline processes. They reduce waste, improve customer satisfaction, and enhance productivity.
This blog aims to demystify Lean and Six Sigma for small warehouses. We’ll explore practical ways to integrate these methodologies into daily operations. Get ready to transform your small warehouse with proven strategies.
What Is the Lean Method?
The lean method focuses on optimizing processes by minimizing waste and maximizing value. It originated in Toyota’s manufacturing plants.
The goal was to reduce costs while maintaining quality. This approach prioritizes continuous improvement and customer satisfaction.
In a small warehouse setting, implementing lean principles can lead to significant improvements. Warehouses can boost efficiency and productivity by identifying and eliminating non-value-added activities.
It includes reducing excess inventory, avoiding overproduction, and minimizing unnecessary goods movement. Some key concepts of the lean method include:
Value Stream Mapping
Value Stream Mapping (VSM) is a powerful tool in the Lean Method Toolkit. It’s like making a map of how things get done in your warehouse, from when an order comes in until it ships out. Think of VSM as a way of a way of drawing a big picture of all the steps involved in getting your product to the customer.
The goal here is to see where you’re doing extra work that doesn’t add value or where there are delays. It’s all about finding the slow spots or the waste-like waiting times, unnecessary moving of goods, or overstocking.
By identifying these, you can start fixing them. Maybe you find out that moving goods from one side of the warehouse to the other is taking too much time. With VSM, you could see how to cut this step out or make it faster.
Just-In-Time Production
Just-In-Time (JIT) production is a key part of the lean method. It’s about making only what is needed when it’s needed and in the amount needed.
Think of it as a super-efficient way to manage inventory. No more, no less. This helps in avoiding too much stuff sitting around and taking up space, or not having enough when it’s needed.
JIT makes sure that all parts of the warehouse work together. When an order comes in, that’s when the product is made or prepared for shipping. It cuts down on wasted time because you’re not making things that nobody wants right now. Plus, it saves money since you’re not buying lots of materials or goods that just sit around.
Kaizen
Kaizen is a Japanese term that means change for the better or continuous improvement. In the context of a small warehouse, Kaizen is all about everyone-from the top managers to the floor workers-coming together to find small ways to make big improvements. Think of Kaizen as a teamwork activity where everyone looks for ways to make their jobs easier and more efficient every single day.
The beauty of Kaizen in warehouses is that it doesn’t need big, expensive changes. It could be as simple as rearranging tools to reduce the time it takes to find them or changing the layout to make moving goods smoother. Small changes, done regularly, add up to significant enhancements over time.
5S
5S stands for five Japanese words that represent steps to organize and maintain a productive workspace. They are sort, set in order, shine, standardize, and sustain. In simple words, think of 5S as a method to keep everything in its right place, clean, and running.
Sort means getting rid of what’s not needed. In a warehouse, this could mean removing old stock or tools that aren’t used anymore.
Set in order is about organizing what’s left. Everything should have its place and be easy to find.
Shine means keeping the area clean. It helps spot any issues, like leaks or wear and tear on equipment, faster.
Standardize is creating rules that everyone follows to keep the first three S’s in place. Sustain is about making this a habit, continuously following these steps to keep everything running well.
Putting 5S into action makes a warehouse neater, safer, and more efficient. It’s all about having what you need, where and when you need it, and keeping things clean and in order. It can save a lot of time and trouble, making sure your warehouse operates.
What Is the Six Sigma Method?
The Six Sigma method aims to reduce defects or errors in processes by using data-driven approaches. This strategy originated in the manufacturing industry but has since been applied to various sectors, including warehousing.
In a small warehouse, Six Sigma principles can help cut errors and improve quality control, resulting in higher customer satisfaction. Some key concepts of the Six Sigma method include:
DMAIC
DMAIC stands for Define, Measure, Analyze, Improve, and Control. Think of it as a step-by-step guide to solving problems and making your warehouse work better. Here’s how it breaks down in simple terms:
Define
It is where you identify the problem. You figure out what’s going wrong or what could be better in your warehouse.
Measure
You gather information. You look at numbers or data to see how big the problem is. It’s like finding out how much time is wasted or how many items are misplaced.
Analyze
You dig deeper. You try to understand why the problem is happening. It’s a bit like being a detective, looking for clues in your data.
Improve
Here’s where you make changes. Based on what you found, you try new ways to fix the problem or make things run smoother.
Control
You keep an eye on things. You make sure the changes you make are working over time. It’s like making sure the solution sticks so the problem doesn’t come back.
Statistical Analysis
Statistical analysis is a big part of the Six Sigma method. In simple words, it’s like using math to figure out problems and make better decisions.
Imagine you’re trying to understand why some orders get shipped out late. Statistical analysis helps you look at all the numbers related to these orders and spot patterns or issues.
This technique uses things like graphs and charts to make complex data easier to understand. For example, a graph might show you that most late shipments happen on Fridays.
With this insight, you can dig deeper to find the cause and fix it. It’s about making sense of lots of information to help your warehouse run better.
Root Cause Analysis
Root Cause Analysis (RCA) is like playing detective with problems in your warehouse. It’s all about asking “why?” again and again until you find the real reason something went wrong. Imagine that you notice that orders are getting messed up.
RCA pushes you to look beyond the obvious and dig deep. You keep asking why the orders are wrong until you find out that your system for tracking inventory isn’t working right.
The goal with RCA is to fix problems for good, not put a band-aid on them. It helps you make sure the same issues don’t keep popping up.
You look at the big picture to find out what’s going on. Then, you can make changes that make a difference. It’s about getting to the bottom of issues so your warehouse runs smoothly.
Standardization
Standardization is all about creating a set playbook for how things are done in your warehouse. Imagine if everyone decided to organize their desk in their way. It might work for them, but it’d be chaos for anyone else trying to find something.
In the warehouse world, standardization means setting up rules that everyone follows, no matter what. It can be about how goods are stored, the way orders are processed, or how returns are handled.
The big win with standardization is that it makes everything predictable and easier to manage. When everyone’s on the same page, there’s less confusion and fewer mistakes. It’s like having a recipe book for your warehouse operations. Once you have these standards in place, training new staff gets simpler, and it’s easier to spot when things go off track.
Integrating Lean and Six Sigma in Your Warehouse
While Lean and Six Sigma are two separate methodologies, they can work hand in hand to improve warehouse operations. The combination of these principles is often referred to as Lean Six Sigma. Here are some ways to integrate both methodologies in your small warehouse:
Start by Identifying Areas for Improvement
The first step to upgrading your small warehouse is finding out what needs work. Look around. See where things slow down or get stuck.
Is it in receiving goods, managing inventory, or shipping orders? Use tools like value stream mapping to spot delays or waste.
Talk to your team. They know their jobs best and can point out problems. Keep track of errors.
Notice patterns where things often go wrong. This step is about knowing your warehouse’s weak spots. Once you see where improvements are needed, you can plan how to make things better.
Use Data to Drive Decisions
Making smart decisions in your warehouse means looking at the numbers. It’s all about using data to see what’s working and what’s not. Think of data as clues that help you solve problems.
For example, when you track how many orders get messed up, you’re collecting important information. It helps you pinpoint where things are going wrong. With this knowledge, you can focus on improving those areas.
Your goal is to boost quality control. The better your data, the smarter your decisions. It means fewer mistakes and happier customers.
Prioritize Continuous Improvement
Continuous improvement is not a one-time thing; it’s about making better changes every single day. It means always looking for ways to do things better, faster, and cheaper without compromising quality.
To know if you are on the right path, you need to use performance metrics. These are like your scorecard, telling you how well your warehouse is doing. Simple things like how quickly orders are filled, how often mistakes happen, or how much waste you’re producing can tell you a lot.
By keeping an eye on these numbers, you can see where you need to improve. It’s like playing a game where the goal is to beat your last score by making your processes leaner and cutting down on errors. Remember, every small change helps make your operations smooth and keep customers happy.
Standardize Processes
Once you’ve found what works for improving your warehouse through Lean and Six Sigma, the next step is to standardize these processes. It means making sure that every part of your supply chain follows the best practices you’ve discovered.
Think of it as setting up rules so everyone works in the best way possible. When everyone in the supply chain knows the right steps to take, things run smoother.
It leads to fewer mistakes, faster shipping times, and happier customers. Standardizing helps make your warehouse’s good days into every day.
Involve and Train Employees
A key part of making your warehouse better is getting your team involved. Teach them about Lean and Six Sigma. Consider enrolling them in online Lean courses to deepen their understanding.
When they grasp these concepts, they can help identify problems and devise solutions. Start with simple training sessions. Break down complex ideas into manageable steps. Show them how their work contributes to the success.
When employees feel like they’re part of the team and understand how they can make a positive impact, they’re more inclined to offer ideas and increase their efforts. A well-trained team is your most valuable asset in enhancing warehouse operations.
Learn More About Lean and Six Sigma Principles for a Small Warehouse
Implementing Lean and Six Sigma in a small warehouse enhances efficiency. These methodologies lead to substantial waste reduction and streamlined operations. Small warehouses can achieve remarkable improvements with focused efforts.
The heart of success lies in continuous improvement and data-driven decisions. Employee involvement and standardized processes further solidify gains.
These strategies transform small warehouses into models of efficiency and reliability. Waste reduction becomes a key achievement in this transformation.
Did you find this article helpful? If so, check out the rest of our site for more informative content.
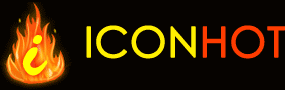