Tech
Safety Considerations When Operating Hydraulic Power Packs

Published
9 months agoon
By
Watson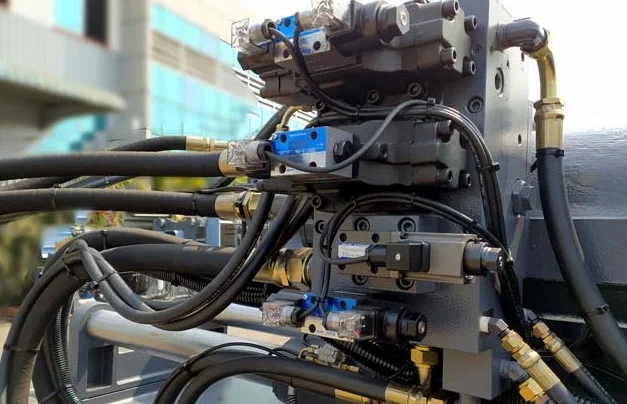
Hydraulic power packs are commonly used in industrial applications to provide pressurised fluid power for operating hydraulic equipment. However, the high pressures and forces involved mean there are important safety considerations operators should keep in mind. Following proper procedures and implementing safety features can help reduce the risk of accidents and injuries when working with these systems.
Perform Regular Maintenance
Conducting thorough, routine maintenance on hydraulic powerpacks such as Zeus Hydratech hydraulic power packs is essential for safety. This includes inspecting hoses and valves for signs of wear or damage, changing hydraulic fluid per the manufacturer’s schedule, replacing filters and breathers when needed, and testing safety valves and pressure switches. Preventative maintenance helps ensure components function properly and don’t fail in hazardous ways during operation.
Use Care When Making Connections
Connecting hydraulic lines between the power pack and equipment requires caution. Make sure the system has fully depressurised before making or breaking any connections. Tighten all couplings and fittings to the proper torque specifications using calibrated torque wrenches. Improperly secured connections can leak high-pressure hydraulic fluid, posing injection hazards.
Implement Safe Working Procedures
Companies should develop and enforce written standard operating procedures for hydraulic power packs. This includes reviewing safety precautions, conducting pre-operation inspections, wearing appropriate PPE, and using lock-out/tag-out procedures when servicing equipment. Operators should be properly trained on procedures and know how to respond in case of a fluid leak, fire, or other emergency.
Have Adequate Hydraulic Fluid Levels
Operating pumps without sufficient hydraulic fluid can cause cavitation, overheating, and damage to the power pack. Make a habit of checking reservoir sight glasses to ensure oil levels are in the proper range before use. Top up with approved hydraulic oils as needed to maintain levels. Having low fluid levels can create hazards.
Use Safety Controls and Devices
Equipment like rupture discs, pressure relief valves, and shut-off valves are critical safety components on a hydraulic power pack system. Make sure these are installed and functioning properly. Pressure gauges also allow operators to monitor the live pressure in the system. Using machine guards can shield operators from hazards as well.
Allow System to Warm Up Under Low Pressure
When starting up a cold hydraulic power pack, the initial start-up pressure should be low. This allows components to slowly warm up to operating temperature before applying full system pressure. Thermal shock at high pressures on cold systems can damage seals and lead to leaks or hose failure.
Address Leaks Immediately
Small leaks left unaddressed can quickly worsen into high-pressure spray emissions. Operators should look for signs of leaks during inspections and have them fixed immediately before resuming work. High-pressure fluid injections are an extremely serious hazard. Address all leaks in a timely manner.
Locate Unit Properly
Hydraulic power packs generate high noise levels during operation. Install these units far from normal working areas as reasonably possible. This helps reduce noise exposure risks for operators. Proper ventilation is also key to avoiding fire hazards. Keep hydraulic power packs located in access-controlled areas free from flammable materials. Adhering to safety procedures and implementing engineered safeguards are key to protecting personnel and equipment when operating hydraulic power packs.
Regular training ensures operators remain mindful of the diverse hazards associated with these systems. Following best practices helps create a safe working environment.
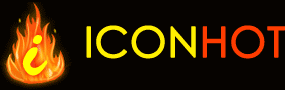