Business
Embracing Efficiency: How Smart Manufacturing Is Transforming Industrial Operations

Published
1 year agoon
By
Watson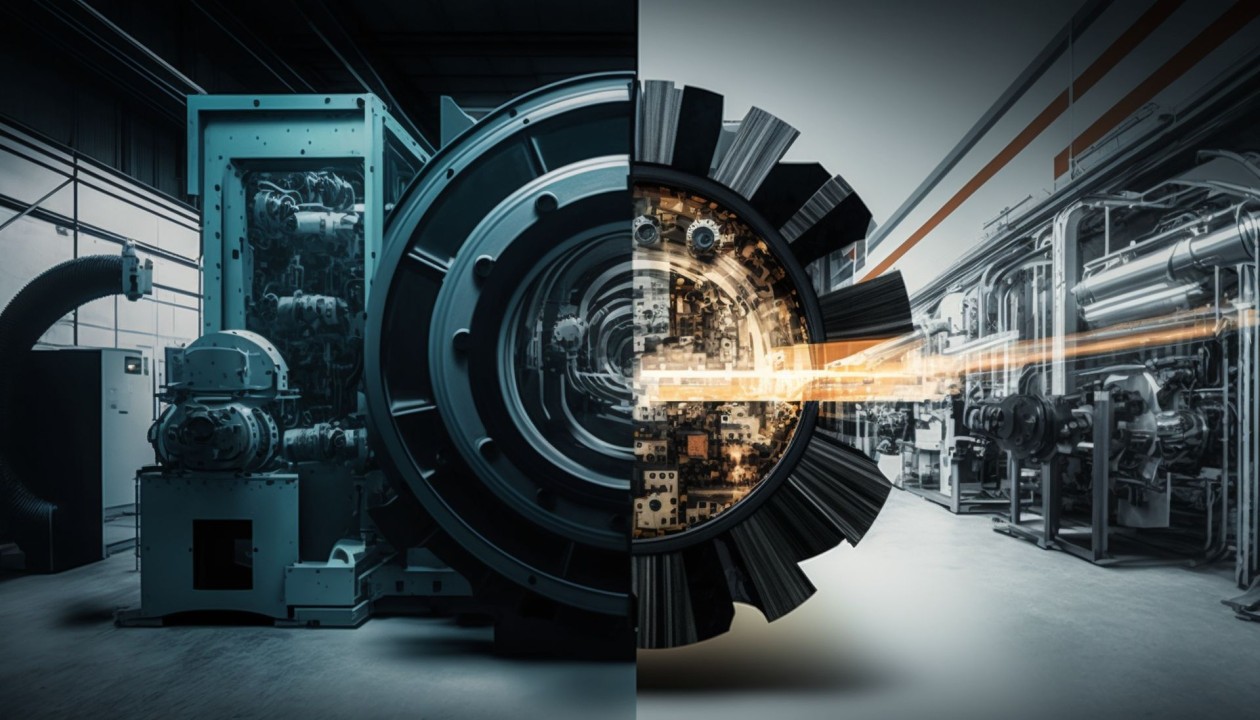
Key Takeaways
- Smart manufacturing is revolutionizing industries with enhanced efficiency and real-time adaptability.
- Core technologies like IoT, AI, and robotics are the driving force behind modern industrial operations.
- Employee engagement and skill development are essential to leverage the benefits of intelligent manufacturing systems.
- Sustainable manufacturing practices result in both environmental and economic advantages.
The Evolution of Industrial Manufacturing
Throughout history, the manufacturing sector has consistently risen to the demands of growing economies, reinventing itself through leaps in technology and production methodologies. Beginning with the mechanization of the textile industry in the 18th century, extending through the mass production era spurred by the assembly line technique, and evolving into the automated precision of today’s robots, the industry has long been a beacon of progress. Notably, each phase has seen manufacturers adapt to emergent technologies to maintain competitive edges, such as the industrial manufacturing software that has become integral to contemporary production strategies. Indeed, the current trend in industrial manufacturing leans heavily towards a digital and automated paradigm marked by smart factories prioritizing seamless integration of systems and real-time data processing. Although digital solutions offer greater precision and efficiency, many in the industry have needed to be faster to shed established legacy systems for fear of disruption or financial loss, which unfortunately hampers potential growth. Recent efforts towards digital transformation have proved that these hurdles can be surpassed, leading to more efficient, adaptable, and cost-effective production methods.
Principles of Smart Manufacturing
At the core of modern industrial evolution lies a concept that feels born from the pages of science fiction: smart manufacturing. Smart manufacturing represents a leap forward, conjuring production ecosystems where machinery and components are interoperable, predictive, and adaptable. Here, Industry 4.0 stands proud as the harbinger of this revolution, employing a suite of technologies that include IoT, AI, and cloud computing in industrial operations. The resultant system is a digital network where machines communicate and collaborate autonomously, driven by data they collect and analyze in real-time. Smart manufacturing blurs the lines between the physical and digital world, enabling a manufacturing landscape that’s flexible and efficient. It introduces a level of agility unheard of with previous iterations of industrial technology. It fosters an environment where systems collect data and use it to predict and adjust to changes in production demands or potential system hiccups almost instantaneously.
Essential Technologies Shaping the Future of Manufacturing
The horizon of futuristic manufacturing is inseparable from the technologies that drive it forward. At the forefront are automation and robotics, which, when paired with industrial manufacturing software, convey efficiency and precision in manufacturing. In factories where time is equivalent to money, robotic systems are integral in performing repetitive and strenuous tasks without fatigue, directly contributing to production scalability.
Furthermore, the holistic adoption of AI and analytics has introduced unprecedented predictive maintenance capabilities in their preventive foresight. Such strategies allow anticipation of potential mechanical failures and operational bottlenecks, enabling pre-emptive rectifications and thus enhanced operational uptime. Augmenting this is the rising influence of additive manufacturing, commonly known as 3D printing, which has expanded the possibilities for custom fabrication, particularly for small runs and complex designs, at a fraction of the cost and time previously required.
Workforce Development and Skills Training
The embrace of intelligent manufacturing tools necessitates concurrent advancements in workforce capabilities. As technology evolves, so must the skill sets required to operate, manage, and optimize these new systems. Success in smart manufacturing is not just about technological investment but also about the investment in human capital, with focused skills training being paramount. More than ever, manufacturers now require technically proficient, adaptive, and comfortable workers in a data-rich environment. Addressing this need, several leading companies have instituted comprehensive training programs that aim to bridge the skills gap.
The Role of Sustainability in Modern Manufacturing
Today’s smart manufacturing initiatives aren’t merely about elevating efficiency and productivity but are increasingly centered around the principles of sustainable practice. The marriage of lean manufacturing techniques with environmental conscientiousness results in operations that are not only profitable but also eco-friendly. Reducing the carbon footprint, optimizing energy usage, and minimizing waste are all hallmarks of smart, sustainable manufacturing strategies. A suite of smart solutions enables manufacturers to carry out detailed life-cycle assessments and streamline their resource allocation, thus contributing to corporate social responsibility targets and satisfying the market’s demand for green products. Having an accurate temperature sensor, such as the one shown here, is one example of how you can be more efficient with your energy usage. This could be applicable to various industries such as chemical processing, food processing and pharmaceuticals. The stories of industry leaders who have successfully adopted sustainable manufacturing practices showcase the dual benefit of environmental stewardship and bottom-line profitability, fostering a new era of eco-industrial excellence.
Overcoming Barriers to Adoption
Moving towards a smart manufacturing model is a significant transition that can be met with challenges and resistance. These challenges often manifest as apprehension about the cost of new technologies, potential disruption to existing workflows, or uncertainty about return on investment. However, these obstacles are manageable. Forward-thinking leaders in the industry have found that clear communication, case studies demonstrating success, and phased implementation help ease the process, creating momentum and proving the value of smart manufacturing investment. Progressive companies approach adoption strategically by engaging stakeholders and cultivating a culture open to innovation. They may pilot new technologies on a small scale to demonstrate efficacy before a company-wide rollout. Such targeted approaches reduce risk and reassure uncertain parties by showcasing real-time improvements.
Global Impact and Economic Considerations
The march towards smart manufacturing is a global movement, with nations at varying levels of development embracing these technologies. This global adoption has given rise to a web of economic benefits, fostering growth and, in some cases, enabling whole regions to skip traditional industrialization stages altogether. Still, as manufacturing relies on automation and intelligent systems, questions arise about the impact on workforces and the economy’s structure. Developing nations, in particular, have a unique opportunity to harness smart manufacturing for rapid economic development. However, they must balance this technology-driven growth with education, employment, and social stability considerations. The conversation also extends to how such advancements affect global trade, potentially reshaping supply chains and trade relationships across nations.
Integrating Smart Solutions for Small and Mid-Sized Manufacturers
Innovative manufacturing solutions aren’t exclusive to industry behemoths; they also offer significant advantages to small and mid-sized enterprises (SMEs). Often more agile than large corporations, SMEs can implement adaptable and scaled smart technologies that give them a competitive edge and enable them to punch above their weight in the global marketplace. By embracing modular and customizable intelligent systems, these manufacturers can enhance their operations’ efficiency and quality, often with more modest investments. Innovation isn’t reserved for large-scale ventures; SMEs can also partake and thrive through the strategic adoption of intelligent factories, advantaging from increased productivity, reduced lead times, and the ability to offer customized solutions that would have been unfeasible under classic manufacturing frameworks.
Looking Ahead: The Next Frontier in Industrial Manufacturing
The future of manufacturing lies in continued innovation and the relentless pursuit of efficiency and sustainability. Industry visionaries are constantly exploring new frontiers, pushing the boundaries of what’s possible through research, development, and the implementation of cutting-edge technologies. Smart manufacturing is not at its zenith; it is a field ripe with potential, promising ongoing transformation that will carry industrial operations into a new era of productivity and eco-awareness. The implications of this technological advancement extend far beyond production lines and factory floors, hinting at a future where industries are symbiotic with natural ecosystems, and manufacturing supports economies and the well-being of communities and the environment. This next frontier in industrial manufacturing beckons us to envision a world where technological prowess and ecological responsibility walk hand in hand, crafting a legacy of smart and sustainable innovation.
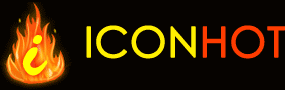