Tech
Using Digital Twin Technology to Drive Predictive Maintenance in Petrochemical Facilities

Published
7 months agoon
By
Watson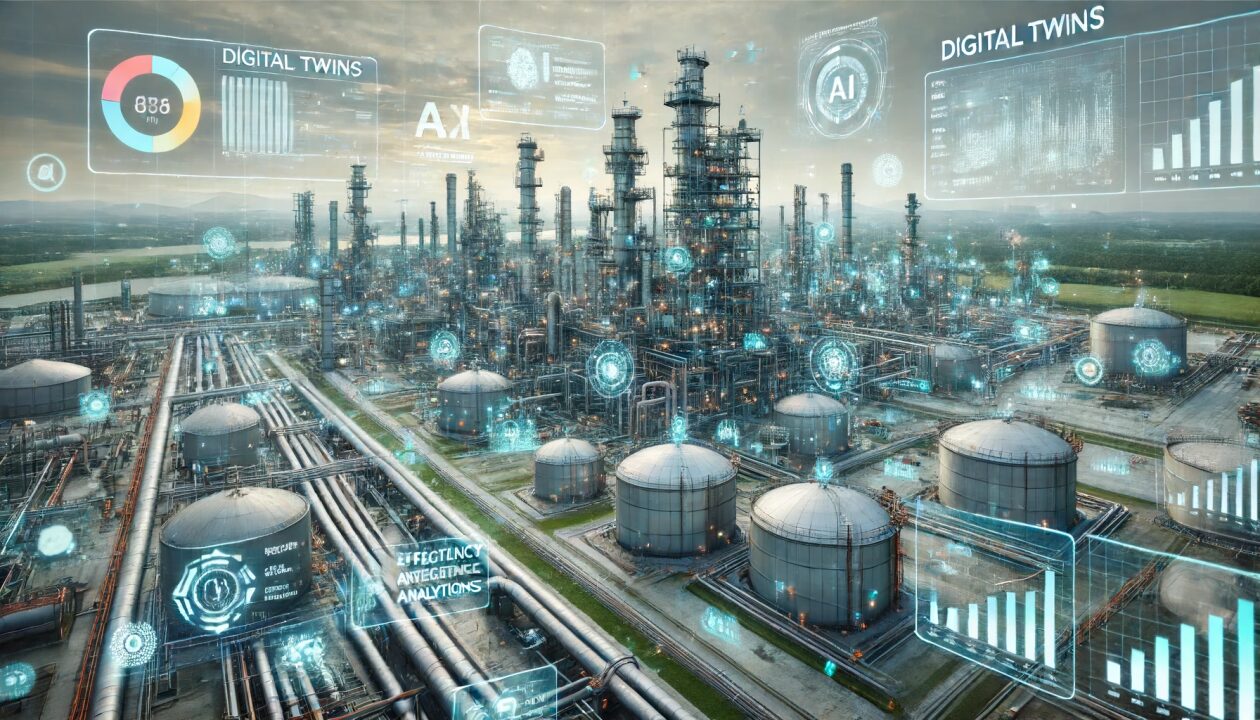
Petrochemical facilities are some of the most complex and valuable industrial environments. With the rise of sophisticated technologies like digital twins, the petrochemical industry can now achieve unprecedented operational efficiency. But what are the tangible benefits of using such technology to drive predictive maintenance in these environments? Let’s explore how these advanced systems are revolutionizing the industry.
Reduced Downtime
One of the primary benefits of digital twin technology in petrochemical facilities is its ability to significantly reduce unplanned downtime. Downtime in these facilities is expensive in terms of lost production, potential safety risks, and repair costs. By creating a real-time digital replica of physical equipment, operators can continuously monitor the performance of machinery, identifying issues before they lead to failures.
This predictive maintenance approach allows companies to schedule repairs during planned maintenance windows. It also ensures equipment is serviced at the optimal time rather than in reaction to breakdowns. The constant monitoring and real-time insights reduce the chances of unexpected failures that could halt production.
Maximizing Equipment Lifespan
Predictive maintenance supported by such technology not only prevents breakdowns but also maximizes the lifespan of critical equipment. Petrochemical facilities rely heavily on machinery that operates under extreme conditions, and replacing or repairing these assets is both time-consuming and costly.
Through continuous data gathering, digital twins provide insights into wear and tear. It offers operators the chance to intervene early. When machinery is maintained based on real-time data rather than time-based schedules, it runs more efficiently and avoids unnecessary stress. This leads to longer equipment lifespans and fewer resources spent on repairs and replacements.
Enhanced Safety and Risk Mitigation
Safety is paramount in petrochemical facilities. Equipment malfunctions or failures can lead to dangerous accidents. Such technology plays an important role in enhancing safety by detecting anomalies in equipment behavior that might indicate potential risks.
Operators can forecast how machinery will behave under various conditions by simulating and testing scenarios within the digital twin, ensuring safer operations. If certain thresholds are exceeded, real-time alerts enable proactive safety measures. This ability to foresee and address problems immediately reduces the likelihood of catastrophic failures, making the workplace safer for everyone involved.
Optimized Maintenance Costs
Maintenance in petrochemical plants can be a significant financial burden, especially when equipment failures occur unexpectedly. However, such technology helps in shifting from reactive to proactive maintenance strategies. This shift reduces the frequency of emergency repairs and helps optimize overall maintenance costs.
With digital twins, maintenance teams can rely on data-driven decisions to prioritize the most critical repairs, use resources more efficiently, and avoid unnecessary interventions. This precision-driven maintenance ensures that only parts needing attention receive attention, leading to significant cost savings over time.
Improved Operational Efficiency
This technology is designed to optimize the performance of industrial assets. In petrochemical facilities, where even minor inefficiencies can have major repercussions, these systems provide a constant flow of data that helps streamline operations. Digital twins help identify bottlenecks and inefficiencies within systems, enabling operators to adjust processes accordingly.
The combination of real-time data analysis and predictive capabilities boosts facility performance overall. This ensures smooth daily operations and promotes long-term strategic improvements, allowing companies to stay competitive in an ever-evolving market.
Boosting Workforce Productivity
Not only does such technology improve machinery performance, but it also empowers the workforce. Maintenance staff no longer need to rely on outdated, time-consuming methods to inspect and repair equipment. Instead, they can leverage data-driven insights from the digital twin to quickly identify problems and apply precise solutions.
With this technology, teams can focus on more strategic tasks rather than spending time on routine inspections or emergency repairs. This boost in productivity translates into more efficient workflows and better use of human resources.
The benefits of using digital twin technology to drive predictive maintenance in petrochemical facilities are clear and transformative. These systems reduce costs and contribute to more sustainable and reliable operations. By anticipating and preventing problems before they occur, petrochemical facilities can ensure the longevity and safety of their assets, creating a safer and more productive future.